Environment
Greenhouse Gas Emissions
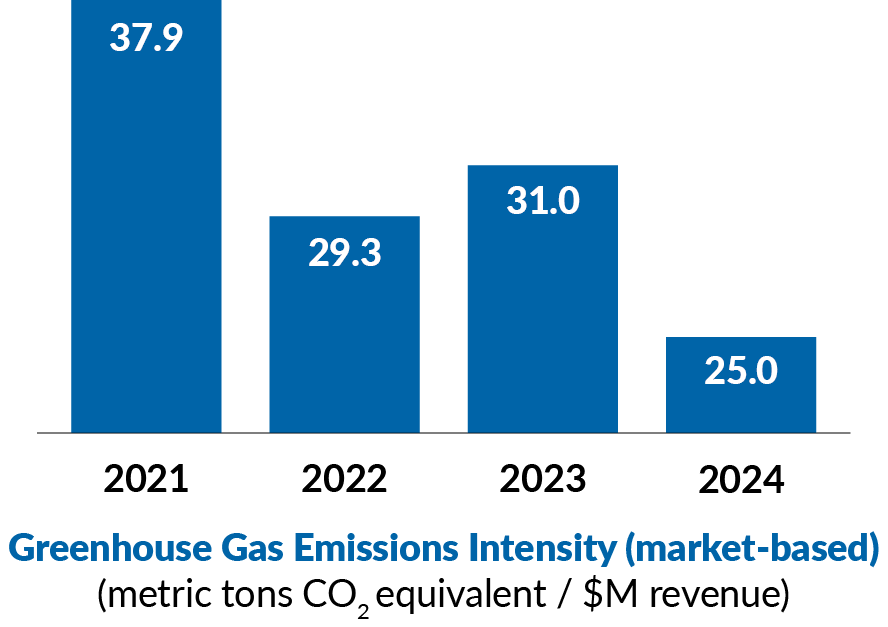
Amphenol is acting to reduce our operational energy use and minimize our greenhouse gas (GHG) emissions through the application of lean production processes and capital investments in energy-saving equipment, which have allowed us to reduce our Scope 1 and 2 GHG emissions intensity. Our renewable energy strategy and GHG reduction efforts have led to a 34% decrease in our revenue-normalized Scope 1 and 2 (market-based) GHG emissions in 2024 compared to 2021, allowing us to achieve or prior goal for a 15% reduction over this time frame. As a result, we have set a new goal to reduce our absolute Scope 1 and Scope 2 (market-based) GHG emissions by 10% by 2030 compared to our 2021 levels.
The use of renewable energy is an important part of our GHG emissions reduction strategy. Over the past few years, the renewable electricity portion of our total energy purchased has increased. We plan to further expand our use of renewable energy in our facilities as we work toward our goal of increasing our use of renewable energy to 50% by 2030.
+ Read about how we are taking action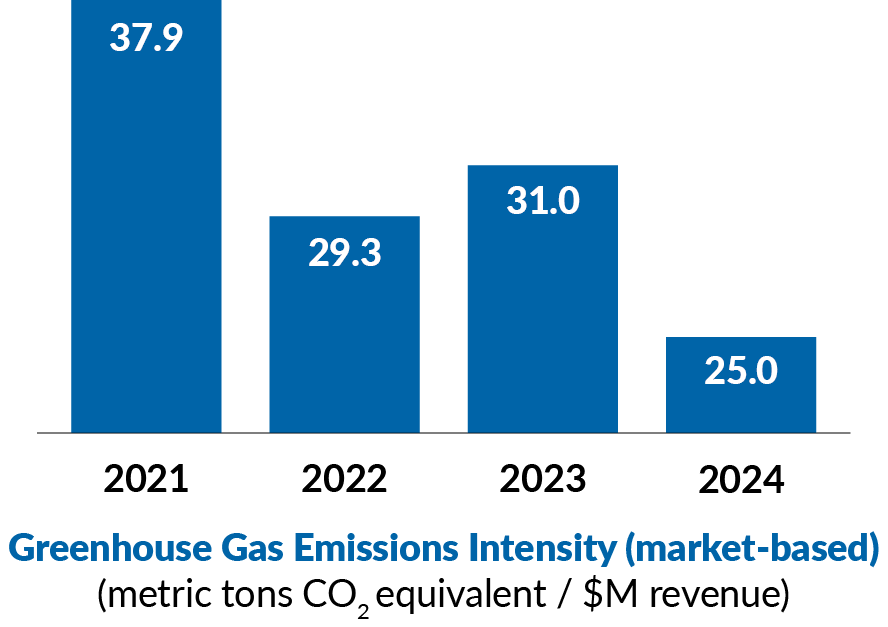
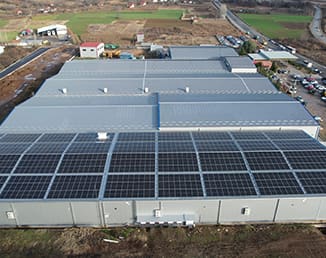
Reducing our Carbon Footprint
Our global facilities continue to support our emissions reduction goals through proactive and innovative actions that reduce their environmental footprint and conserve resources, while at the same time helping our facilities save on energy costs. To support these goals, several Amphenol facilities have installed on-site solar panels to increase their renewable electricity consumption and decrease their dependency on fossil fuels. These installations have helped provide a continuous, stable and clean source of energy for their facilities. In addition, our successful solar installments at some facilities have inspired other Amphenol businesses to consider increasing their renewable energy consumption.
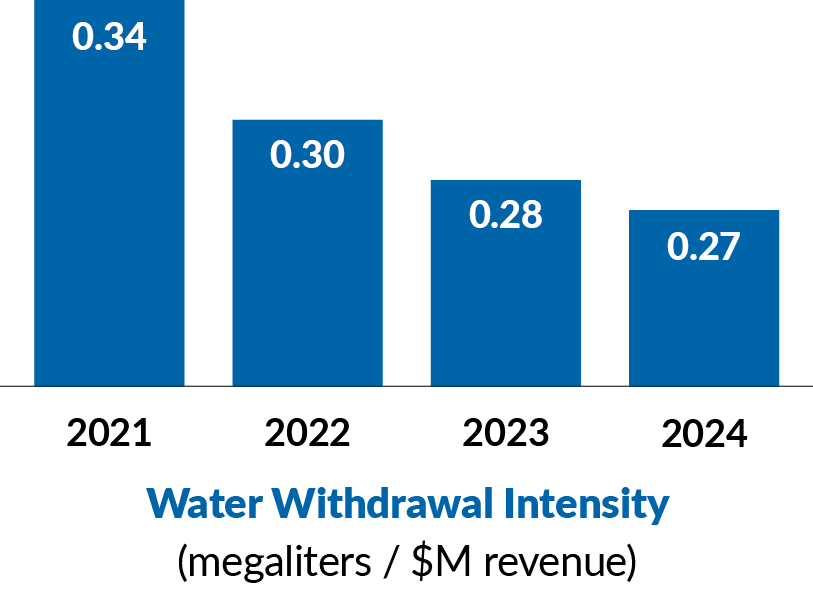
Water Use
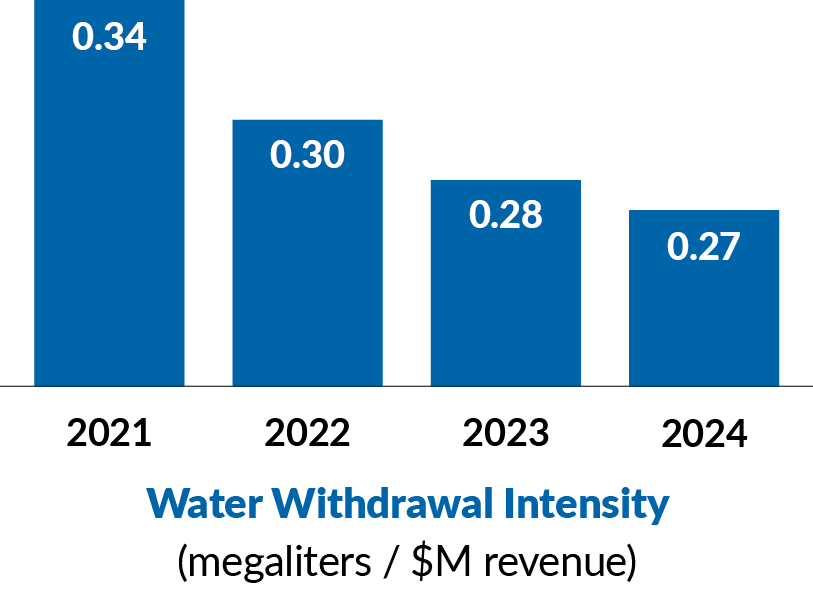
Amphenol’s manufacturing processes do not require a significant amount of water, however we do strive to be as responsible as possible with the water we use. In order to reduce our overall water usage, we pursue water optimization projects across our facilities and have invested in systems to reuse and reclaim our wastewater. Through our continued actions and investments, we were able to reduce our water withdrawal intensity by 4% in 2024 versus the prior year. Since 2017, our actions have resulted in our water withdrawal intensity declining by 40%, a 7% compound annual reduction over this seven-year period.
We plan to continue to explore new opportunities for improvement in our water usage across our global footprint. To support our commitment, we have set a goal under SDG 6.4 Clean Water and Sanitation. By the end of 2030, Amphenol will reduce total water withdrawal of our top 20 facilities by 15% versus 2021 levels.
+ Read about how we are taking action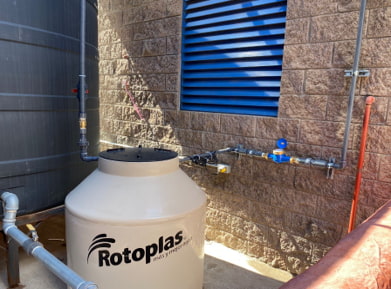
Limiting Our Water Use
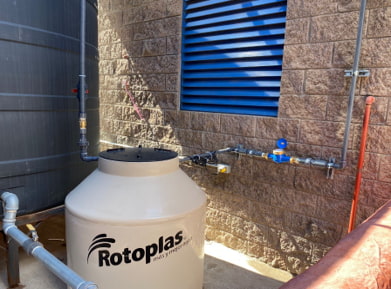
At our facility in Nogales, Mexico, our team is working to enhance water efficiency and minimize water waste. The facility has developed a water recovery system that redirects water to the facility’s fire suppression system’s main reserve tank. In addition, the team has introduced a return loop in its plating processes to help the facility use less externally sourced water. All of these actions have helped the facility reduce its overall water withdrawal by 15%.
Waste Disposal
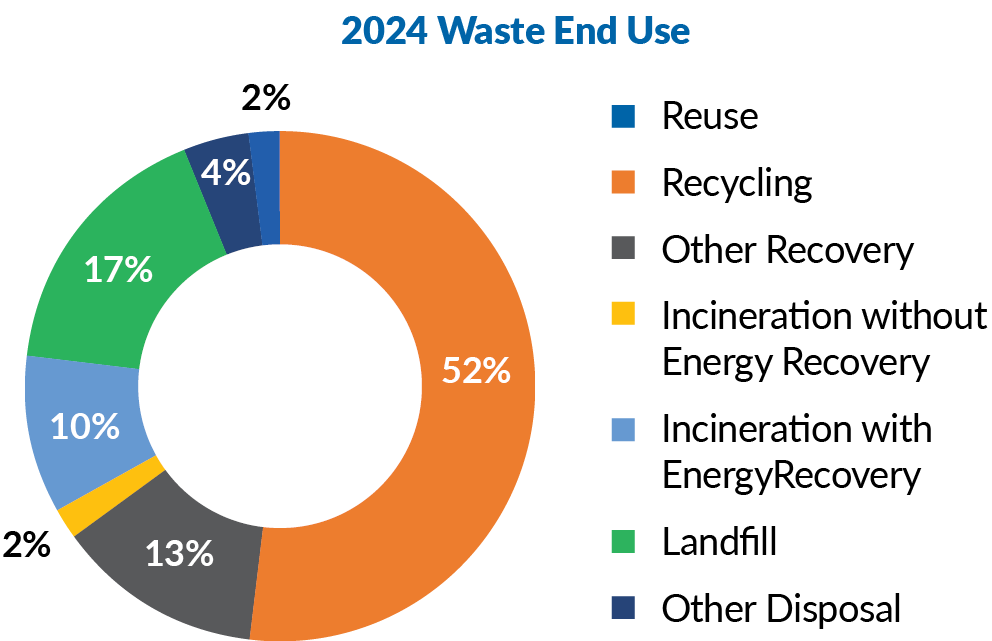
Limiting our use of resources and minimizing our waste remain a core component of Amphenol’s operational management culture. Our operations employ a number of methods to limit our waste, with some examples including utilizing recycled packaging for connectors, regrinding thermoplastics as appropriate to supplement virgin material feedstocks, composting organic material from our employee cafeterias and reducing our paper usage. As a result of our efforts, we were able to reuse, recycle or recover 67% of our total waste in 2024. We will continue to look for new ways to minimize our material use as we work to further reduce our waste production and deliver more sustainable products to our customers.
+ Read about how we are taking action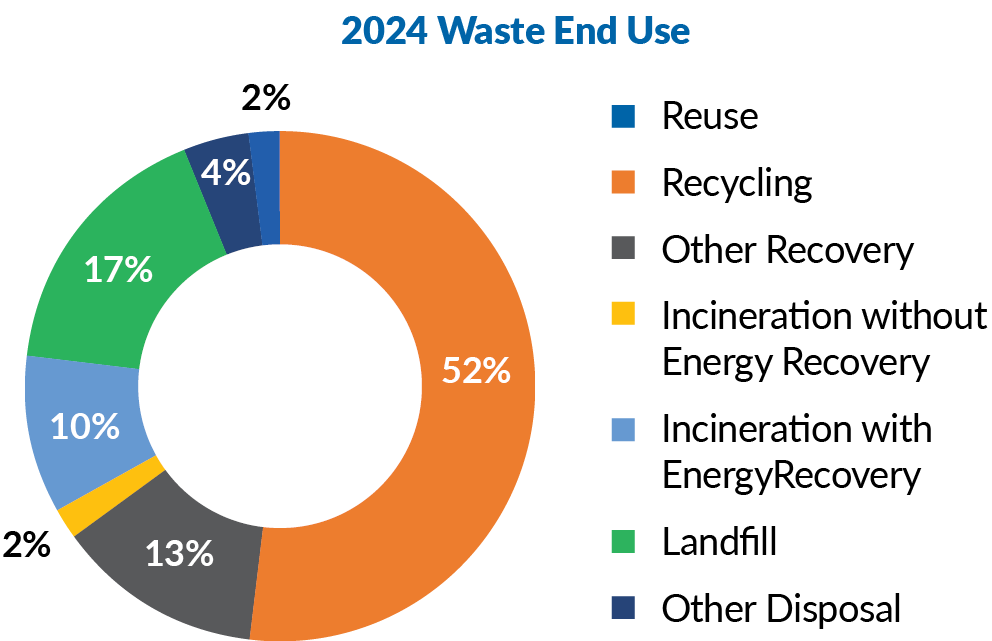
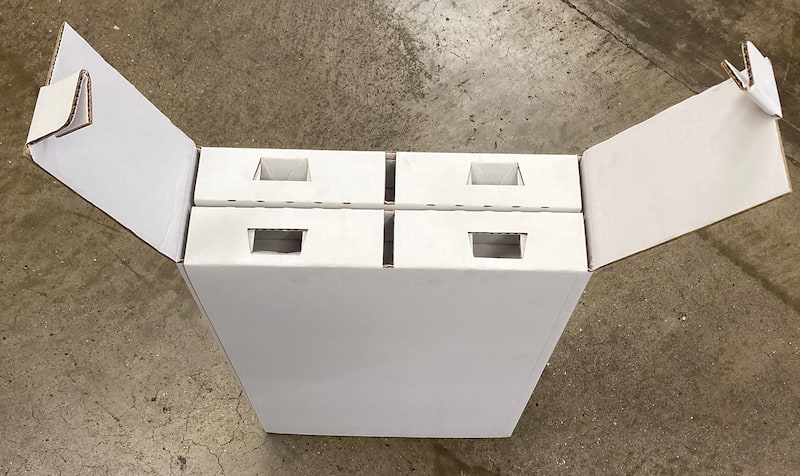
Reducing Packaging Waste
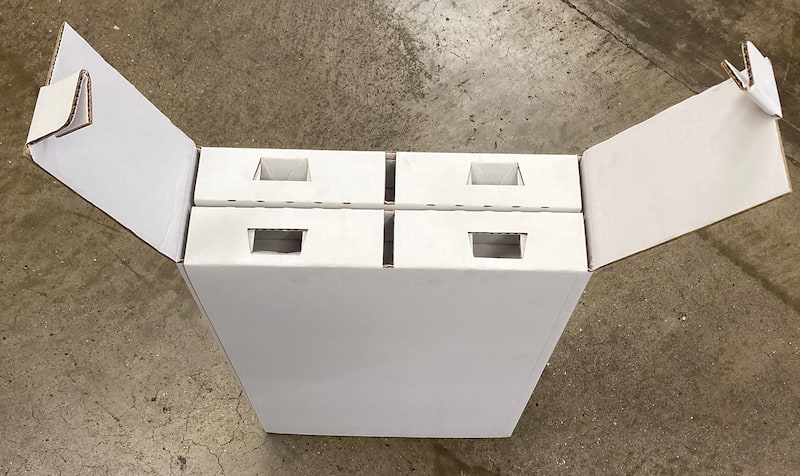
As part of our commitment to reducing waste and improving sustainability, our team in Wellingborough, UK, has taken a major step toward eliminating plastic from its antenna packing process. To achieve this, the team engaged employees across departments to contribute ideas, collaborated with customers to better understand their needs and worked closely with our cardboard packaging supplier to develop viable solutions. As a result of the process, the team redesigned its packaging to eliminate plastic dividers, protective foam and plastic bags to hold smaller parts. By 2025, the facility will no longer use any plastic in its packing process, and the team in the UK plans to share these learnings with their teams in Denmark and Macedonia.